D1.6: Analytical methods for building components
Summary
Research on calculation and analytical methods for MEP/HVAC components concentrates on developing a methodology
to prevent common errors on MEP systems and improve the building’s indoor environmental quality and energy
performance. The methodology covers the full building process, from prefabrication and construction to the in-use phase
and maintenance. The methods apply for new buildings, as well as for refurbishment and maintenance projects. The
main objectives of this deliverable are:
- To define quantitative analytical methods for performance assessment of building components;
- To determine the calculation of KPIs regarding the overall performance of MEP/HVAC systems;
- To eliminate the difficulties in assessment and analysis by introducing conceptual self-inspection protocols for
quality assessment and supporting instruments;
- Recommendations for implementation of the inspection process.
This deliverable presents the research outcomes on performance assessment, frequent construction errors, key
performance indicators and relevant standards specific for MEP/HVAC components affecting the quality and
performance of energy-efficient buildings (EeB). The focus of this deliverable is on calculation and analytical methods for
MEP/HVAC components.
The self-inspection process
The self-inspection process is integrated in INSITER’s 8 step methodology. This methodology describes a detailed
procedure where newly developed methods, tools and techniques (MTTs) contribute to INSITER’s goal to close the gap
between design and realization. Self-inspection on MEP/HVAC components takes place in different steps of the
methodology and in different phases throughout the building process. Figure 1 depictures these inspections and the
time-interval concerned.
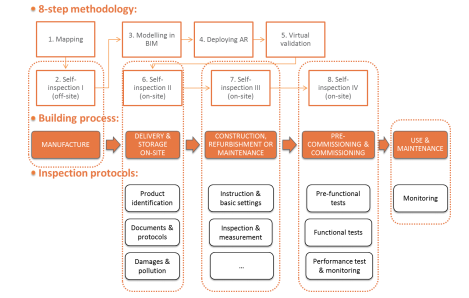
Figure 1: Inspections for MEP/HVAC components during the different building phases
All inspections revolve around the same concept: to eliminate errors that have a major influence on a definite list of KPIs.
Because of the complex multitude of actions, INSITER’s methodology will follow a structural approach. This method
follows the concept of eliminating errors ‘top down’ and ‘bottom up’ concurrently, or so-called ‘up-stream’. The levels of
inspection are defined as ‘components’, ‘subsystems’, and ‘systems’ van bottom to top. The inspections are executed
during the successive phases and system-specific proceedings of the realization phase.
Common errors are classified in one of the following categories (type of error):
01. The component is damaged or polluted
02. The wrong component is installed
03. The component is installed incorrectly
04. The component is provided with the wrong settings
Critical MEP/HVAC systems affecting EeB performance
Four leading MEP systems are elaborated for self-inspection, together covering for over 90% of all MEP systems with a
relation to indoor environment and energy usage. These systems are:
- Heating & cooling (with heat pump);
- Mechanical ventilation (with heat recovery);
- Solar hot water;
- LED lighting.
The systems are described in detail, presenting their components and related common errors that we see in construction
projects today. The mentioned errors lead to deviations on INSITER’s KPIs, and obviously, need to be eradicated. Every
component has standalone functionality and will eventually work like a cog in a machine. Errors or mismatches that
won’t get solved as soon as possible in the process have a good chance to get covered up, making it hard or almost
impossible to discover. So INSITER’s job is, to detect errors and solve them before it is too late. This is exactly how the
inspections work; they will be executes at a certain level (component, subsystem or system), on a particular time in the
process and with a technique that is associated to the type of error. These three elements play a crucial part in the
inspections of MEP/HVAC components.
Furthermore, every MEP system has its own specific function and therefore all MEP systems are being provided with
their own individual measurements and calculations. All the defined measurements and calculations have a clear relation
with one or more KPIs. Where MEP systems interconnect, assessment is performed for all systems related. For
example, the temperature in the occupied zone is being influenced by the heating system, but most of the time also by
the ventilation system. In that case, measurement of this temperature is carried out with the aim to assess the heating
system, as well as the ventilation system.
Conceptual self-inspection protocols for MEP/HVAC components
Basically, self-inspections for MEP components start at delivery on-site. MEP components are hardly prefabricated, and
if they are, inspection can be executed as if it were a single component. In case a component or range of components
(like piping) is prefabricated at the factory, inspection will start there. More often we see pipelines and duct systems
integrated in prefab elements. They will be subject to inspections as part of the prefab element, before being transported
to the building site. The first inspections on-site will be to make sure the right component is delivered and that it is
flawless. These are visual inspections, making use of INSITER tools on a mobile device.
After delivery, the components will be transported to their location of mounting, in the building. More inspections will be
executed to make sure the right component will be installed at the right place in the right manner. Again, the MEP worker
is using the INSITER tool on his mobile device to perform the inspections.
When installation of a component or subsystem is completed, another visual check with a mobile device is executed, to
make sure the component is installed the right way. INSITER provides information from BIM with guidelines and
inspection protocols to help the MEP worker on-site. The next step is to make sure the control settings will be applied as
intended, making this the final check on component level.
At this time the commissioning phase has started. Inspections are moved to subsystem and system level and
measurements are being carried out to assess the performance of the (sub) system. Meanwhile, monitoring tools will be
integrated in the control system, to start monitoring the performance. While measurements are carried out, results will be
compared to the design model in BIM and deviations are being quantified. A feedback loop will make sure that
corrections will be constantly checked and evaluated.
Total building quality and further research
The interaction of MEP components with building component takes place from day 1. Whether MEP components are
integrated in building elements, or installed in the building as single components. Performance of the building will always
depend on both. So during inspections, for example, checks will take place on the connections of MEP components with
building elements. Sometimes intended, to seal off lead-throughs, or unintended, to prevent the transfer of vibrations.
As construction is forwarding, constant comparison and evaluation to the BIM model is making sure deviations to the
design will stay within limits. This will be executed for the building elements, as well as the MEP systems. Then, when
the building is coming close to completion, a simulation tool (like Vabi, see chapter 4) will take over and will be used to
assess the overall performance of the building. The process is being visualized in
Figure 2: Illustration of the assessment of total building performance
During this process, continues quantification is being carried out by calculation and analysis of MEP/HVAC components
and systems. The next step for INSITER is to qualify the results with the aim to decide whether a deviation should lead
to corrections. This will be elaborated and defined in the follow-up deliverable within the INSITER project.
Download